Keep Your Line Running Smoothly with Reliable Packaging Machine Repair
Keep Your Line Running Smoothly with Reliable Packaging Machine Repair
Blog Article
The Ultimate Guide to Packaging Maker Fixing: Maintain Your Operations Running Efficiently
Comprehending the intricacies of product packaging equipment repair service is crucial for maintaining optimum performance and minimizing disturbances. Routine upkeep not just extends the life of these equipments however likewise addresses typical concerns that can restrain productivity.
Relevance of Routine Upkeep
Routine maintenance of product packaging devices is important for making certain optimum efficiency and longevity. By applying a structured maintenance routine, operators can determine potential problems before they intensify right into considerable troubles. This aggressive technique not only lessens downtime but likewise expands the lifespan of the tools, ultimately causing reduced operational prices.
Regular assessments allow for the evaluation of essential elements such as sensors, belts, and seals. Dealing with damage promptly avoids unanticipated failings that could interrupt manufacturing and bring about costly repair work. Furthermore, regular upkeep aids ensure compliance with market criteria and laws, fostering a safe working atmosphere.
Additionally, upkeep tasks such as lubrication, cleansing, and calibration substantially boost equipment efficiency. Improved performance converts to consistent item top quality, which is vital for maintaining customer complete satisfaction and brand credibility. A well-kept packaging device operates at optimal rates and lowers product waste, adding to general efficiency.
Common Packaging Machine Concerns
Product packaging makers, like any type of complicated machinery, can encounter a variety of usual problems that may hinder their efficiency and effectiveness - packaging machine repair. One common problem is irregular securing, which can result in product perishing and waste if packages are not properly secured. This commonly results from misaligned components or used sealing components
One more frequent concern is mechanical jams, which can happen due to international items, worn components, or improper placement. Jams can trigger delays in manufacturing and increase downtime, inevitably impacting total efficiency. Additionally, digital malfunctions, such as failing in sensors or control systems, can lead and interrupt procedures to incorrect dimensions or unpredictable machine habits.
Furthermore, problems with product feed can additionally arise, where products might not be provided to the product packaging area constantly, causing disruptions. Wear and tear on belts and rollers can lead to suboptimal efficiency, needing prompt attention to stop more damage.
Comprehending these usual concerns is important for preserving the honesty of product packaging procedures, guaranteeing that machinery runs efficiently and successfully, which in turn helps in meeting manufacturing targets and keeping item quality.
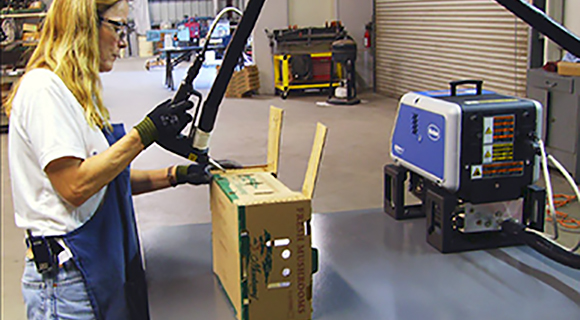
Fixing Techniques
Reliable fixing techniques are crucial for immediately dealing with concerns that occur with packaging equipments. A methodical approach is crucial for identifying the source of breakdowns and reducing downtime. Begin by collecting information concerning the symptoms observed; this might consist of unusual sounds, functional delays, or mistake codes displayed on the maker's interface.
Next, describe the device's guidebook for fixing standards specific to the design concerned. This resource can supply valuable understandings right into common issues and advised diagnostic steps. Make use of aesthetic evaluations to look for loose connections, used belts, or misaligned parts, as these physical factors commonly add to operational failures.
Apply a process of elimination by screening specific machine functions. For example, if a seal is not developing correctly, examine the securing device and temperature settings to identify if they satisfy functional requirements. Document each step taken and the results observed, as this can aid in future troubleshooting efforts.
Repair vs. Replacement Decisions
When confronted with equipment malfunctions, deciding whether to fix or change a product packaging device can be a complex and critical choice. This choice depends upon a number of essential factors, consisting of the age of the equipment, the degree of the damage, and the predicted impact on operational performance.
To start with, think about the device's age. Older machines might need Going Here more constant repair work, leading to greater advancing expenses that can exceed the financial investment in a brand-new device. Furthermore, evaluate the extent of the breakdown. Minor issues can usually be dealt with promptly and affordably, whereas considerable damages could demand a considerable monetary commitment for repairs.
Operational downtime is an additional important factor to consider. If repairing the equipment will trigger long term delays, spending in a brand-new device that uses enhanced performance and dependability could be more prudent. Moreover, take into consideration the availability of parts; if replacement elements are difficult ahead by, it might be a lot more strategic to replace the device completely.
Eventually, carrying out a cost-benefit analysis that includes both long-lasting and instant ramifications will help in making a notified decision that aligns with your financial restrictions and functional goals. (packaging machine repair)
Precautionary Steps for Longevity
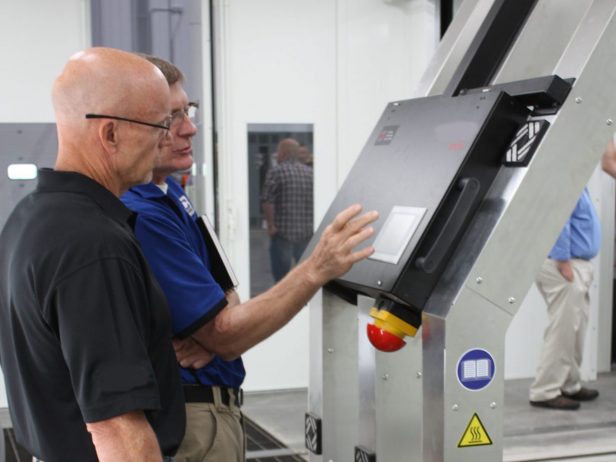
Key preventive steps include routine lubrication of moving parts, positioning checks, and calibration of controls and sensing units. Developing a cleansing timetable to get rid of debris and contaminants from machinery can considerably decrease deterioration (packaging machine repair). Furthermore, keeping track of operational specifications such as temperature and vibration can assist discover irregularities early
Training personnel to acknowledge indications of wear or read what he said malfunction is another essential component of preventive maintenance. Equipping operators with the knowledge to carry out basic troubleshooting can lead to quicker resolutions and minimize functional disturbances.
Paperwork of maintenance activities, consisting of solution records and evaluation findings, fosters responsibility and helps with informed decision-making regarding replacements and repairs. By focusing on precautionary steps, businesses can guarantee their product packaging devices run at peak efficiency, ultimately resulting in increased performance and decreased functional expenses.
Conclusion
In final thought, the efficient upkeep and repair of packaging makers are extremely important for sustaining operational effectiveness. By implementing precautionary actions, businesses can enhance device durability and make sure nonstop productivity in packaging operations.
Understanding the complexities of packaging maker repair service is critical for maintaining ideal performance and lessening interruptions.Routine upkeep of packaging makers is critical for making certain optimum efficiency and long life.Product packaging equipments, like any kind of intricate equipment, can experience a selection of common problems that might hinder their efficiency and performance. If fixing the maker will certainly trigger extended delays, spending in a brand-new machine that offers boosted performance and dependability may be more sensible.In verdict, the efficient maintenance and repair of product packaging makers are vital for sustaining functional performance.
Report this page